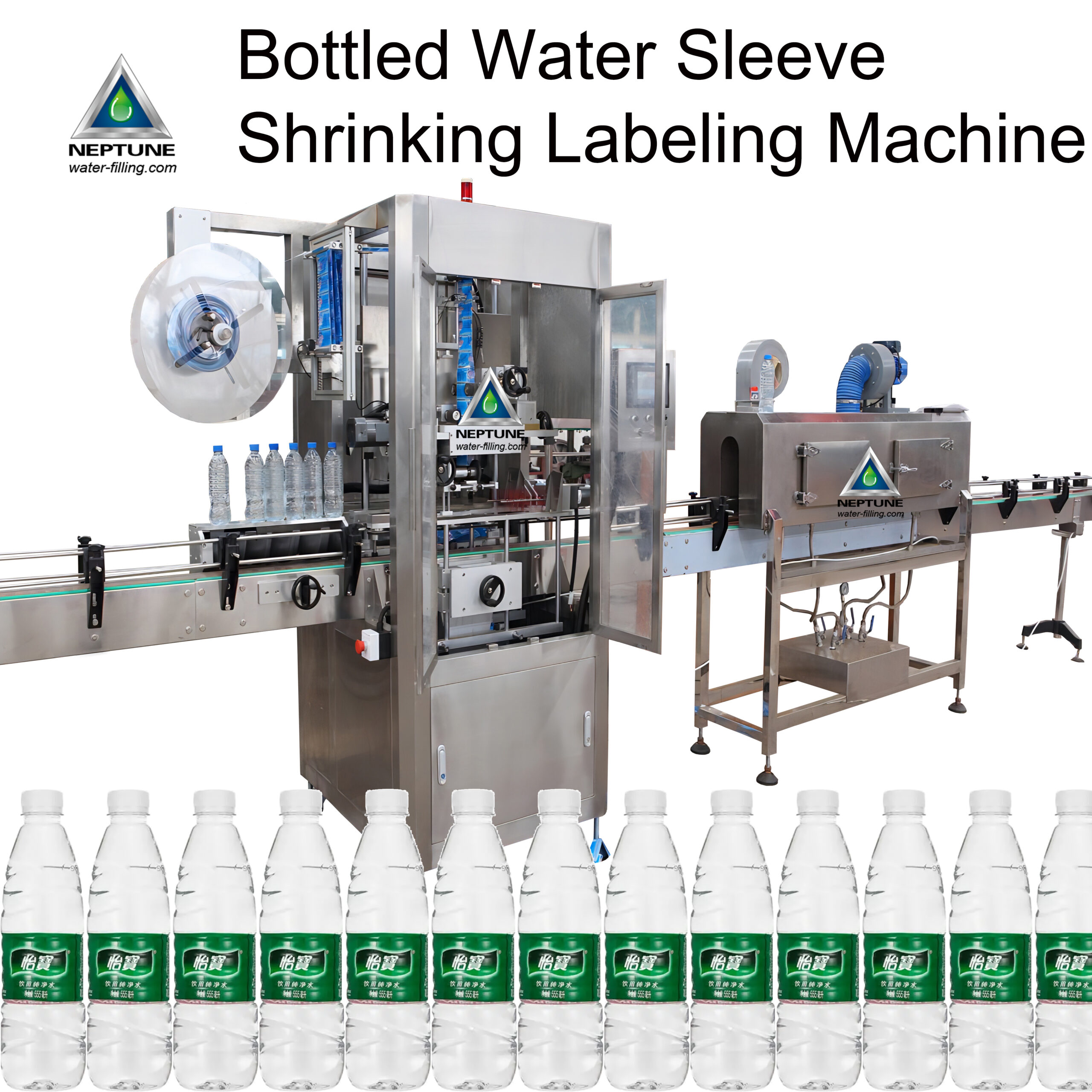
Parameter
Input Power 3.0KW
Input Voltage 380V/50Hz
Production Efficiency 9000bph
Main machine dimension 2200L×1100Wx2000H
Applicable diameter of bottle body 28mm~125mm
Applicable length of label 30mm~250mm
Applicable thickness of label 0.03mm~0.13mm
sleeve labeling machine with a scan system operates as follows:
- Bottle Inspection:
- Bottles move along a conveyor belt, passing through the sleeve labeling machine.
- The scan system, equipped with sensors or cameras, reads information on each passing bottle. It may include barcode scanning, label positioning, or other relevant details.
- Label Application:
- Based on the scanned information, the sleeve labeling machine instantaneously applies a PVC label onto each bottle.
- The label is typically a pre-printed or pre-cut sleeve that is placed over the bottle.
- Brusher Positioning:
- After label application, a small brusher system is employed to ensure the proper positioning and smoothing of the label on the bottle.
- This step helps in eliminating air bubbles and ensuring the label adheres uniformly to the bottle surface.
- High-Temperature Shrinking Tunnel:
- Labeled bottles then pass through a high-temperature shrinking tunnel.
- The tunnel uses hot air or steam to heat the PVC labels, causing them to shrink tightly around the contours of the bottle.
- Label Shrinkage:
- The high temperature activates the shrinking properties of the PVC labels, resulting in a snug fit around the bottle.
- The label conforms to the shape of the bottle, providing a seamless and visually appealing appearance.
This process ensures that each bottle receives a precisely applied and securely shrunk label, contributing to the overall packaging aesthetics. The automated nature of the scan system and labeling machine enhances efficiency and accuracy in the labeling process.
Sleeve shrink labeling machine process
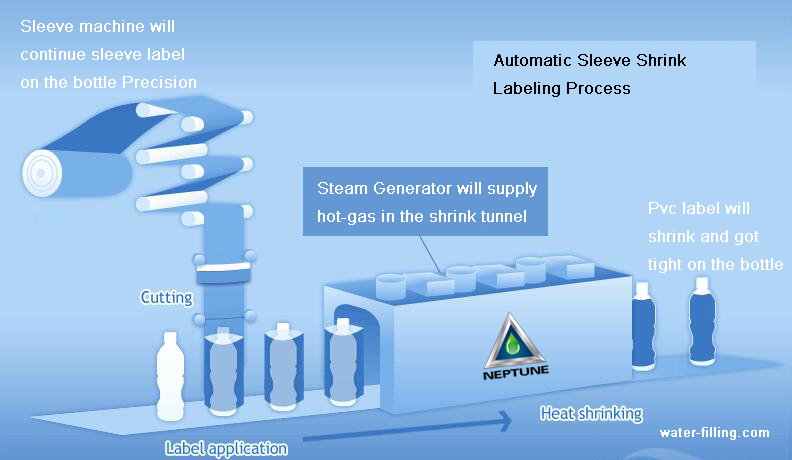
The sleeve shrink labeling machine process typically involves several steps:
- Bottle Placement:
- Empty bottles are fed onto a conveyor belt, which transports them through the labeling machine.
- Label Dispensing:
- PVC sleeves or labels are dispensed from a roll or stack and positioned to be applied to the passing bottles.
- The labels are placed over the bottles in a loose manner, allowing for easy passage through the machine.
- Label Application:
- As the bottles move forward, the labels are pulled tightly around them.
- Heat, steam, or hot air is applied to the labels, causing them to shrink and conform to the shape of the bottles.
- This process ensures that the labels adhere securely to the bottles without wrinkles or air bubbles.
- Label Shrinkage:
- The heat source in the machine activates the shrink properties of the PVC material, causing it to contract and tightly wrap around the bottles.
- The labels shrink uniformly, providing a smooth and professional appearance on the bottles.
- After the labels have been shrunk onto the bottles, they pass through a cooling zone where air is blown over them to accelerate the cooling process.
- This helps to set the labels firmly in place and ensures that they maintain their shape.
Overall, the sleeve shrink labeling machine process offers an efficient and effective way to apply labels to bottles, providing a professional and attractive finish to the packaged products.
Video of the automatic sleeve label shrinking labeling machine.
Introduce
1.Shrinkage film volume label rack, match with adjustable device, convenient to adjust according to differ volume label 5″~10″paper tube.
2.Simply installation, Easy for both square and round bottle.
3.Rotary mechanism is easy to adjust.
4.Unique pressing sleeve labeling method, convenient and reasonable.
5.Auto controlling feeding system, level-off shrinkage film materials and regulate/adjust strain simultaneity.
6.Unique design knife plate, within specification cope, can avoid changing knife base, knife changing is quick and conveniently.
7.Middle guide-pole clip system can make it easy to change shape mold.
8.Label location system, can promote and demote in-phase adjust location according to specific bottle type requirement.
9.High-sensitivity photoelectric, label cutting precision is highly.
10.Stainless steel electric equipment controlling case.
11.Use advanced man-computer Interface auto controlling technology. All key electric component use international famous industrial brand.